Helmet Test Rig Anvil Finish
P. David Halstead
Summary: This paper on test rig anvil finishes was prepared by Dave Halstead for the May 2003 ASTM headgear meeting. Anvil finish is important for anvils that may penetrate more into a helmet if they are smooth, and particularly if lubricated by water from a wet sample. Dr. Halstead's paper explores the issues, but since the legal requirement for bicycle helmets is to pass the CPSC standard, and CPSC uses chromed anvils, the issue was settled, and no spec for anvil finish was written into the ASTM F1446 (test methods) or F1447 (bicycle helmet) standards.
This subject seems very straightforward. However, the surface finish of the anvil may dramatically affect the performance of a anvil and the resultant test. To fully control the quality of machining, it is necessary to evaluate the surface texture of the part piece. The specific surface finish of a part is important to define. In the US the surface finish is measured in millionths of an inch, called a Microinch. 1 Microinch = 0.000,001 inch.
Surface peaks and valleys: centerline
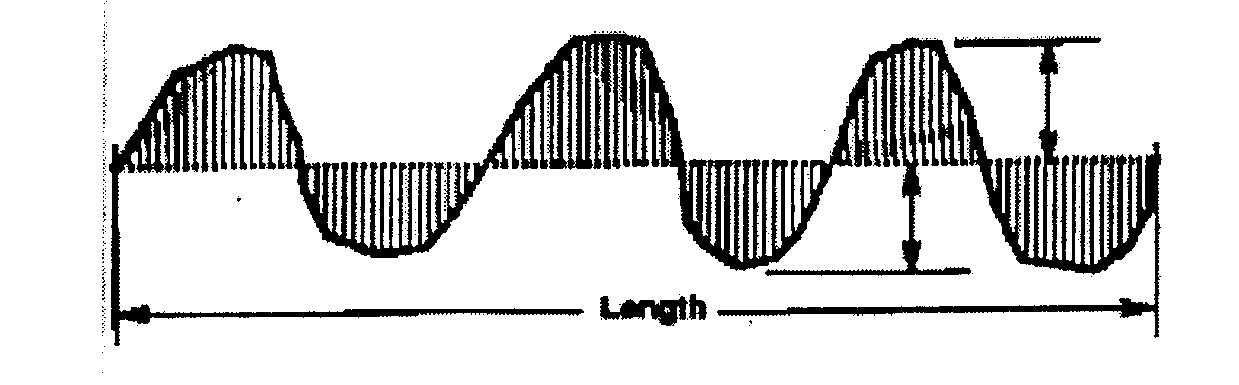
Examples of surface finishes produced by various manufacturing processes.
-
2 Micro = lapped and polished gage blocks
-
4 Micro = chrome type finish or burnished part
-
6-8 Micro = best ground finish normally achievable
-
16 Micro = standard ground finish
-
16 Micro = best turned/milled finish
-
64 Micro = good machined finish
-
125 Micro = standard machined finish
- 250 Micro = rough machined finish
Measurement of surface finish
Surface finish is made up from the irregularities of a part surface in a given length. A procedure is then applied to evaluate the depth and height of this surface.The evaluation of a machined finish requires a special inspection machine called a Profilometer. This machine utilizes a fine stylus probe to explore the surface of the part. The surface finish is made up from the spacing of these peaks and also the surface area within these peaks.
A calculation is required to determine the center line average of the part surface. This is called the CLA and is internally calculated by the surface inspection Profilometer machine, the results will be shown in Ra values.
The term Ra refers to the Roughness Average. This is a mathematical average of the surface above and below the centerline in comparison to a linear distance.
Issues:
- Currently we do not define the finish for impact anvils. It has been demonstrated that variations in finish can have a noticeable effect on the testing of helmets. We replicated this kind of variation and found the general statements as follows to be true.
- For some conditions and anvils, (wet hemi, or hazard), the smoother the anvil the more potential for damage that might lead to helmet failure.
- For flat anvils on some impact locations a smooth anvil leads to a reduction in g.
- In all cases our testing showed that the difference in helmet pass fail is of importance only on helmets that might be termed as close to failure in any case. Or marginal when tested to the existing protocol.
Complication:
The government's lab (CPSC) apparently uses chrome finished anvils and many may feel other non-government labs must follow this lead even though the standards are not clear on this.Specifying a chrome finish typically of about 4 micro inches Ra would result in almost every anvil in any busy lab to be out of spec most of the time.
Suggestion:
Anvil surfaces must be of a finish from 125 micro inches to 64 micro inches. Any good machine shop should be able to reach this range without special grinding, lapping or polishing, but it is still a smooth surface that will be demanding in the test but easily repaired and maintained. Yes that means the government will have to buy new anvils. Testing indicates that variation in test data within this finish range will not be an issue. Anvils should not be lubricated at the time of testing.BHSI Note:
See our Visit to the CPSC Lab page for photos of CPSC's anvils.Back to the top
Back to the Home Page